Turbocharger
BPS team is the first Iranian engineering team engaged with design and development of Turbocharger in Iranian national engines.
The development started from 2008 in EF7 engine and D87engine and passed all validation stages.Iranian OEM policies are engine downsizing, targeting update Euro emission standard and minimizing fuel consumption. For realizing OEM targets, BPS team continues development for other OEM project, which will launch according to Customer’s plan.
Oil Module for EF7 engine
Oil Module is a compact and high performance Oil/Water cooling, filtering and oil pressure measuring system.
This system maximized filtering area with minimum packaging for installation. Filter concept is environment friendly and allow quick service filter change. Production of EF7 oil modules has been one of BPS’s core competences. Thanks to the integration and use of state of the art materials; especially of high performance plastics and rubbers, significant cost and weight savings can be achieved.
Hydraulic power steering pump (405)
Hydraulic actuators add controlled energy to the steering mechanism, so the driver can provide less effort to turn the steered wheels when driving at typical speeds, and reduce considerably the physical effort necessary to turn the wheels when a car is stopped or moving slowly.
Power steering can also be engineered to provide some artificial feedback of forces acting on the steered wheels.
Representative power steering systems for cars augment steering effort via an actuator, a hydraulic cylinder. These systems have a direct mechanical connection between the steering wheel and the linkage that steers the wheels. This means that power-steering system failure (to augment effort) still permits the car to be steered using manual effort alone.
Hydraulic power steering systems work by using a hydraulic system to multiply force applied to the steering wheel inputs to the vehicle’s steered road wheels. The hydraulic pressure typically comes from a rotary vane pump driven by the vehicle’s engine.
Hydraulic power steering pump (206)
Hydraulic actuators add controlled energy to the steering mechanism, so the driver can provide less effort to turn the steered wheels when driving at typical speeds, and reduce considerably the physical effort necessary to turn the wheels when a car is stopped or moving slowly.
Power steering can also be engineered to provide some artificial feedback of forces acting on the steered wheels.
Representative power steering systems for cars augment steering effort via an actuator, a hydraulic cylinder. These systems have a direct mechanical connection between the steering wheel and the linkage that steers the wheels. This means that power-steering system failure (to augment effort) still permits the car to be steered using manual effort alone.
Hydraulic power steering systems work by using a hydraulic system to multiply force applied to the steering wheel inputs to the vehicle’s steered road wheels. The hydraulic pressure typically comes from a rotary vane pump driven by the vehicle’s engine.
Hydraulic power steering pump (R2)
Hydraulic actuators add controlled energy to the steering mechanism, so the driver can provide less effort to turn the steered wheels when driving at typical speeds, and reduce considerably the physical effort necessary to turn the wheels when a car is stopped or moving slowly.
Power steering can also be engineered to provide some artificial feedback of forces acting on the steered wheels.
Representative power steering systems for cars augment steering effort via an actuator, a hydraulic cylinder. These systems have a direct mechanical connection between the steering wheel and the linkage that steers the wheels. This means that power-steering system failure (to augment effort) still permits the car to be steered using manual effort alone.
Hydraulic power steering systems work by using a hydraulic system to multiply force applied to the steering wheel inputs to the vehicle’s steered road wheels. The hydraulic pressure typically comes from a rotary vane pump driven by the vehicle’s engine.
Hydraulic power steering pump (EF7)
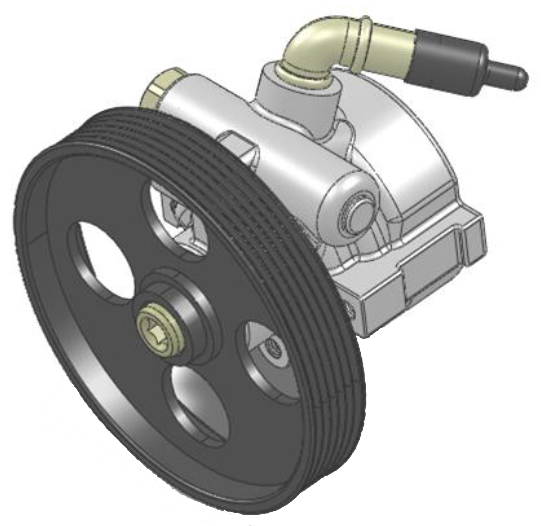
Hydraulic actuators add controlled energy to the steering mechanism, so the driver can provide less effort to turn the steered wheels when driving at typical speeds, and reduce considerably the physical effort necessary to turn the wheels when a car is stopped or moving slowly.
Power steering can also be engineered to provide some artificial feedback of forces acting on the steered wheels.
Representative power steering systems for cars augment steering effort via an actuator, a hydraulic cylinder. These systems have a direct mechanical connection between the steering wheel and the linkage that steers the wheels. This means that power-steering system failure (to augment effort) still permits the car to be steered using manual effort alone.
Hydraulic power steering systems work by using a hydraulic system to multiply force applied to the steering wheel inputs to the vehicle’s steered road wheels. The hydraulic pressure typically comes from a rotary vane pump driven by the vehicle’s engine.
Water pump XU7
Other type of engine water pump developed by BPS team and produced in mass scale such as XU7 water pump.
Water pump for EF7 engine
EF7 Water pump is a part of Oil Module, which packaged by design limitation and designed with optimum efficiency and minimum weight.
This part manufactures and assembles by BPS since 2009 with highest quality standard level and minimum manufacturing cost. All manufacturing stage traced via barcoding system for fulfilling traceability requirement. Manufacturing process implemented mistake proof methods to avoid any non-conformity in final product. BPS engineering team designed and equipped water pump testing facilities. The testing equipment are validated by OEM as a neutral test center to service other water pump manufacturing companies.
Dump valve
Dump valve is an emergency outlet for the compressed air in the after turbocharger compressor.
Solenoid valve
A boost controller is a device to control the boost level produced in the intake manifold of a turbocharged engine by affecting the air pressure delivered to the waste gate actuator.
CVVT Continues Variable Valve Timing
Variable valve timing (VVT) is the process of altering the timing of a valve lift event, and is often used to improve performance, fuel economy or emissions.
It is increasingly being used in combination with variable valve lift systems. Iranian OEM emissions regulations targets; is the main cause for using CVVT in their New Engine roadmap. Therefore, BPS team started study engineering concept and supply from reputable CVVT manufacturer in first stage and planned for localization.